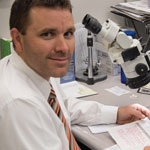
A Crown is Not Just a Crown.
Aesthetic Dentistry recently spoke with Arrowhead Dental Laboratory’s CAD/CAM manager, Jay Nelson, about monolithic full zirconia restorations, also known as ZirCrowns. Jay and his team developed a unique process that results in a highly aesthetic zirconia restoration. He recently shared his insights about the process with us.
AD: WHAT IS A ZIRCROWN?
JN: ZirCrown restorations are full zirconia restorations, and they are a compelling option for dentists from two perspectives—strength and aesthetics.
AD: WHAT ARE THE DIFFERENCES BETWEEN ARROWHEAD’S ZIRCROWN AND ZIRCONIA CROWNS MADE BY OTHER LABS?
JN: The material is zirconia, but the fabrication of it—the actual manufacturing of it—has been improved, and this process leads to a more aesthetic outcome. Doctors are requesting more and more ZirCrown restorations. During the past couple of years, Arrowhead’s internal team has refined and perfected the manufacturing process of these full zirconia crowns.
AD: WHAT’S NEW ABOUT THE PROCESS OF MAKING THESE CROWNS?
JN: At Arrowhead Dental Laboratory, we’ve done a lot of research about how to fabricate ZirCrowns. We tested and tried out several methods until we developed a process that led to the highly aesthetic result that we knew our customers would appreciate. Our research included a lot of trial and error. The different processes that we tried all offered varying results.
One of the things we learned is that the latest technology and traditional fabrication techniques could be combined. The result was a precision fit with CAD/CAM techniques, in addition to the highly aesthetic outcome.
We designed the crowns on software that can create a natural-looking morphology and anatomy in the crown. We create the crown to have the proper color, the proper shading, the gingival warming, and the incisal translucency—all of which are traditionally difficult to achieve in a full contour zirconia (without the porcelain). With the new process, we achieve all of the benefits with custom green state shading. The result is a full zirconia crown that offers traditional strength as well as incisal translucency.
The process at Arrowhead is very specialized. Each ZirCrown is a custom order, made by master technicians. We are particularly proud of our enhanced staining technique, which starts with a master technician infiltrating the green state of the zirconia prior to sintering (firing). We actually brush on the stains of the final shade before it’s sintered.
The staining effect is infused into the restoration itself, rather than merely being brushed onto the surface. The result is aesthetics that are more lifelike and longer-lasting than those produced by stains that were applied after the sintering process.
Arrowhead has tremendously skilled technicians, and it is to their credit that they have developed this unique process. It is exciting to see the results of precision technology combined with the skill and artistry of the human touch.
AD: WHAT ROLE DO ARROWHEAD’S TECHNICIANS PLAY IN THIS PROCESS?
JN: Our CAD designers are equipped with the latest production technologies, and they receive ongoing education from leaders in the industry as the technology continues to evolve. One of our Elite technicians works with the CAD designers to ensure that their design conforms to the Arrowhead standard and not just a predefined setting in the software. The level of care in both the design process and the milling process is something that we take great pride in.
Before the staining process, our technicians contour the restoration by hand after it has been milled in the green state. A technician takes a handpiece and fine-tunes the anatomy of the restoration, contouring the embrasures or contouring the height of the crown.
Arrowhead’s ceramists contour the crown prior to the stainers working on the restoration in the green state. Again, the advantage of staining prior to the green state is that the color is saturated throughout the entire restoration, not just painted on after the restoration has been sintered.
We have three employees who stain the zirconia crowns at Arrowhead. The lead stainer has been with the lab for about 15 years. Our process is unique because the stainers can’t see the result of the final shade until after it comes out of the oven.
So how do we achieve a particular A2 shade or VITA shade when we don’t see a result until 3 or 4 hours later? That’s where the experience of our stainers is crucial—they know what they’re doing and they know what to look for because they’ve done the process many times.
My department has stained thousands of crowns various ways, with a number of different brushstrokes. We’ve fired them and logged every detail of the entire process until we learned exactly what worked. We developed a process that can match whatever particular shade a dentist requests. If a dentist is looking for something unique, we have the skills, talent, and experience to deliver that particular, customized shade.
We also have a quality assurance team that is second-to-none. The evaluation criteria and requirements for approval of one of these crowns are some of the most stringent in the industry. Their expertise in evaluation is a critical component to the iterative improvement of our process, and their insights were key to the development of this process.
AD: PLEASE EXPLAIN WHAT THE TECHNICIANS DO FROM START TO FINISH ON AN ARROWHEAD ZIRCROWN?
JN: First, we scan the models into our CAD program. We have multiple designers who design these ZirCrowns on our CAD software, specifically detailing the morphology of the tooth. Then we send the design to a CAM unit where we calculate the milling path of the crowns. Next, we put the design into a milling machine where the crown is milled out of the material.
Once the crown goes through the initial milling process, the hand-contouring of the crown begins. We remove any sprues by hand, and if it’s an anterior tooth or a bridge, we fine-tune the contours of it prior to staining. If it’s a single posterior restoration, we go straight into staining the crown.
After staining, the crown is then sintered for the appropriate time to maximize the beauty of the staining process. When it comes out of the oven, we check the fit on the working die(s) and the occlusion on the working model to make sure everything, including the contacts, looks good.
When the fine-tuning is finished, if there are additional adjustments needed, we will dial in the contacts and make whatever additional tweaks are necessary. Lastly, we polish the crown or apply a little surface staining, based on the final shade of the restoration.
AD: WHAT ARE THE DOCTORS GETTING FOR THEIR MONEY WHEN THEY BUY A ZIRCROWN FROM ARROWHEAD?
JN: When doctors buy a ZirCrown from Arrowhead, the technicians spend a lot of time to ensure that the quality of the crown is superior. They ensure that the stain is correct, the shade is correct, and that the contours are perfect for the patient. The technicians really take their time to make sure these crowns look as lifelike as possible.
The value of an Arrowhead ZirCrown comes from the technicians who are spending the time necessary to create a crown with superior aesthetics. It shows in the final product. In today’s marketplace, many dentists are looking for ways to stand out from every other dentist in town. The Arrowhead ZirCrown is a great way to do just that.
AD: ARE THERE OTHER ADVANTAGES TO ARROWHEAD’S ZIRCROWN PROCESS?
JN: I think another advantage is the longevity of the crown, not just structurally but aesthetically. Arrowhead’s ZirCrowns are built to last and they will look great for the life of the restoration.
In today’s competitive environment, dentists should look at any advantage that can separate them from other dentists. Offering ZirCrown is a natural, easy way to stand out because it offers patients a crown that has been customized to their mouth and crafted just for them.
Dentists who want to stay competitive should offer something above market—above what’s commonplace—and Arrowhead’s ZirCrowns are above and beyond what you see in zirconia crowns offered by other labs. We are not taking these crowns right out of a machine, slathering some surface color on them, and shipping them off. That’s why we say a crown is not just a crown.
With Arrowhead’s ZirCrown process, we’re taking the benefit of both modern technology, and the artistry and precision of human expertise to create something more unique, natural, and lifelike. There are human fingerprints on this product—people are actually touching it, shaping it, and creating something that looks like it naturally exists in the mouth, rather than a mass-produced piece of dentistry. The results are the highest aesthetics possible combined with the strength of full zirconia. It’s a beautiful combination.
AD: WHAT IS THE OVERALL VALUE OF AN ARROWHEAD ZIRCROWN?
JN: In a word, craftsmanship. In today’s marketplace, zirconia crowns have become a mass-produced product that really doesn’t offer a dentist the ability to differentiate the cosmetic outcomes that he or she can deliver for patients. This is not the case at Arrowhead. We have taken the time and effort to create a zirconia crown that has all the benefits of zirconia without having to compromise on aesthetics. Helping our dentists develop a competitive advantage is just as important to us as the product itself.
One of the best things about Arrowhead is its focus on craftsmanship. Other labs might consider the ZirCrown to be a “no-frills” type of product, but Arrowhead sees it as an opportunity to bring value above and beyond what is expected.
The fact that we have been encouraged to invest so much time and effort into the development of this process is a testament to Arrowhead’s focus on delivering life-changing dentistry to every patient. It is a process that we are very proud of, and one that I believe makes a difference in the lives of dentists and patients alike.